Magnetic coupling is a fascinating method of transmitting torque between shafts without direct physical contact, relying instead on magnetic fields. The significant technology is pivotal in applications requiring hermetic sealing or where traditional mechanical couplings might falter.
In this comprehensive exploration, we’ll delve into the principles, types, applications, advantages, and comparisons between magnetic couplings and traditional couplings.
Key Takeaways
- Magnetic coupling enables torque transfer without physical contact, using magnetic fields for efficient power transmission.
- It’s ideal for applications requiring hermetic sealing, such as in chemical, pharmaceutical, and food processing industries.
- There are several types of magnetic couplings—disc-type, synchronous, and canned couplings—each suited to specific use cases.
- Neodymium magnets are commonly used due to their high magnetic strength, making couplings more compact and powerful.
- Compared to traditional couplings, magnetic couplings offer reduced wear, lower maintenance, leak-proof operation, and misalignment tolerance.
- Magnetic couplings can also act as a safety feature by slipping under overload conditions, preventing equipment damage.
- Their non-contact nature makes them highly valuable in contamination-sensitive and hazardous environments.
1. What Is Magnetic Coupling?
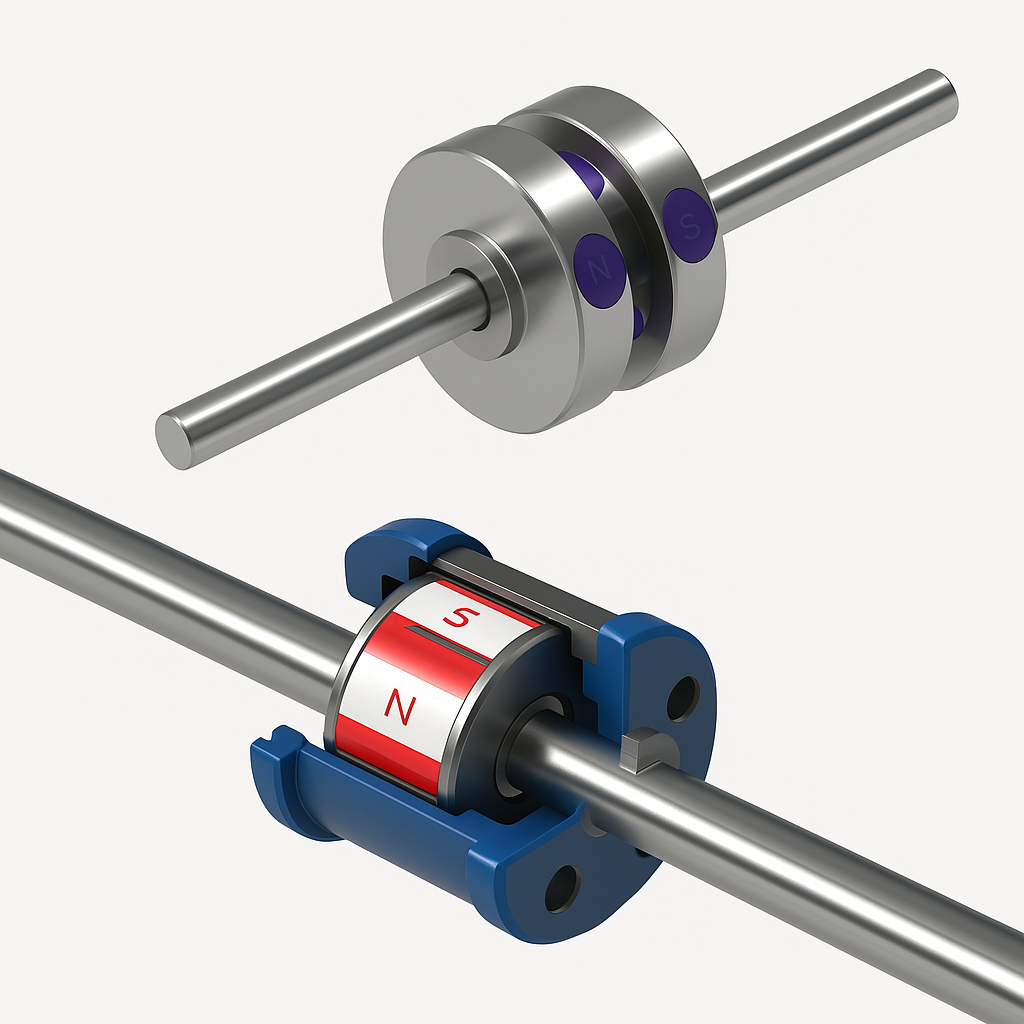
At its core, magnetic coupling involves the transfer of rotational force between two shafts through magnetic fields, eliminating the need for direct mechanical links. It is achieved by aligning magnets on both the driving (input) and driven (output) components. When the driver rotates, its magnetic field influences the driven component to rotate synchronously, effectively transmitting torque across a physical gap. The non-contact transmission is especially beneficial in environments where maintaining a sealed barrier is crucial, such as in pumps handling corrosive or hazardous fluids.
2. How Magnetic Couplings Work?
The operation of a magnetic coupling hinges on the interaction between magnetic fields generated by permanent magnets or electromagnets arranged on two separate rotors. These rotors are positioned such that their magnetic fields interact across an air gap or a non-magnetic barrier. As the driving rotor turns, its magnetic field induces a corresponding rotation in the driven rotor, allowing torque to be transmitted without physical contact. The mechanism not only facilitates effective torque transfer but also accommodates certain misalignments between shafts, enhancing the flexibility and durability of the system.
3. Types of Magnetic Couplings
Magnetic couplings come in various designs, each tailored to specific applications and operational requirements. The primary types include:
Co-Axial Magnetic Couplings
Co-axial couplings consist of two concentric rotors equipped with magnets arranged to face each other directly. The configuration allows for efficient torque transmission through an intervening barrier, such as a containment shell in a pump. Co-axial couplings are renowned for their ability to maintain a hermetic seal, making them ideal for applications involving hazardous or sterile fluids. They also exhibit high torque capacity and can accommodate minor misalignments.
Disc-Type Magnetic Couplings
Disc-type couplings feature two opposing discs embedded with magnets. Torque is transmitted through the air gap between these discs. The design is particularly versatile, allowing for angular misalignment of up to 3 degrees and parallel misalignment up to 0.25 inches while still transmitting nearly full rotational torque. Disc-type couplings are often employed in applications like magnetic mixers and pumps where flexibility and ease of maintenance are priorities.
Synchronous Magnetic Couplings
In synchronous couplings, the driver and driven magnets are aligned to allow direct torque transmission through magnetic attraction and repulsion. These couplings maintain a fixed speed ratio between the shafts, making them suitable for applications requiring precise torque transfer. Their synchronous operation ensures consistent performance, which is critical in processes demanding high accuracy.
Eddy Current Magnetic Couplings
Eddy current couplings utilize magnetic fields to induce eddy currents in a conductive material, creating a resistive force that enables torque transmission. Unlike synchronous couplings, they allow for slip between the driver and driven components, which can be advantageous in applications requiring controlled torque limiting or soft starts. However, the slip can lead to energy losses and heat generation, necessitating careful consideration in design.
4. Applications of Magnetic Couplings
Magnetic couplings are employed across a diverse range of industries due to their unique advantages:
- Chemical and Pharmaceutical Industries: In environments where contamination must be avoided, magnetic couplings enable the operation of mixers and agitators without breaching sterile or hazardous barriers. It ensures product purity and operator safety.
- Food and Beverage Processing: Maintaining hygienic conditions is paramount in food production. Magnetic couplings facilitate the operation of equipment like mixers and conveyors without direct contact, reducing the risk of contamination.
- Automotive and Aerospace: In electric vehicles and aircraft, magnetic couplings improve motor efficiency and reduce wear in drivetrain systems. Their ability to function without lubrication and withstand high speeds makes them suitable for these demanding.
- Industrial Automation: Conveyor systems and robotic arms benefit from magnetic couplings’ ability to transmit torque without physical contact, allowing for smoother operation and reduced maintenance.
5. Advantages of Magnetic Couplings
The adoption of magnetic couplings offers several notable benefits:
Elimination of Mechanical Seals
By transmitting torque through magnetic fields, these couplings remove the need for mechanical seals, which are prone to wear and leakage enhancing the reliability and lifespan of equipment.
Leak Prevention
The hermetic sealing capability of magnetic couplings is crucial in preventing leaks of hazardous or sterile substances, ensuring environmental safety and compliance with stringent industry regulations.
Reduced Maintenance
The non-contact nature minimizes wear and tear, leading to lower maintenance requirements and operational downtime. It translates to cost savings and increased productivity.
Tolerance to Misalignment
Magnetic couplings can accommodate certain degrees of angular and parallel misalignment, reducing the need for precise alignment during installation and operation.
Intrinsic Overload Protection
In the event of an overload, magnetic couplings can slip, providing a form of torque limiting that protects both the motor and the driven equipment from damage.
6. Magnetic Couplings vs Traditional Couplings
When comparing magnetic couplings to traditional mechanical couplings, several distinctions emerge:
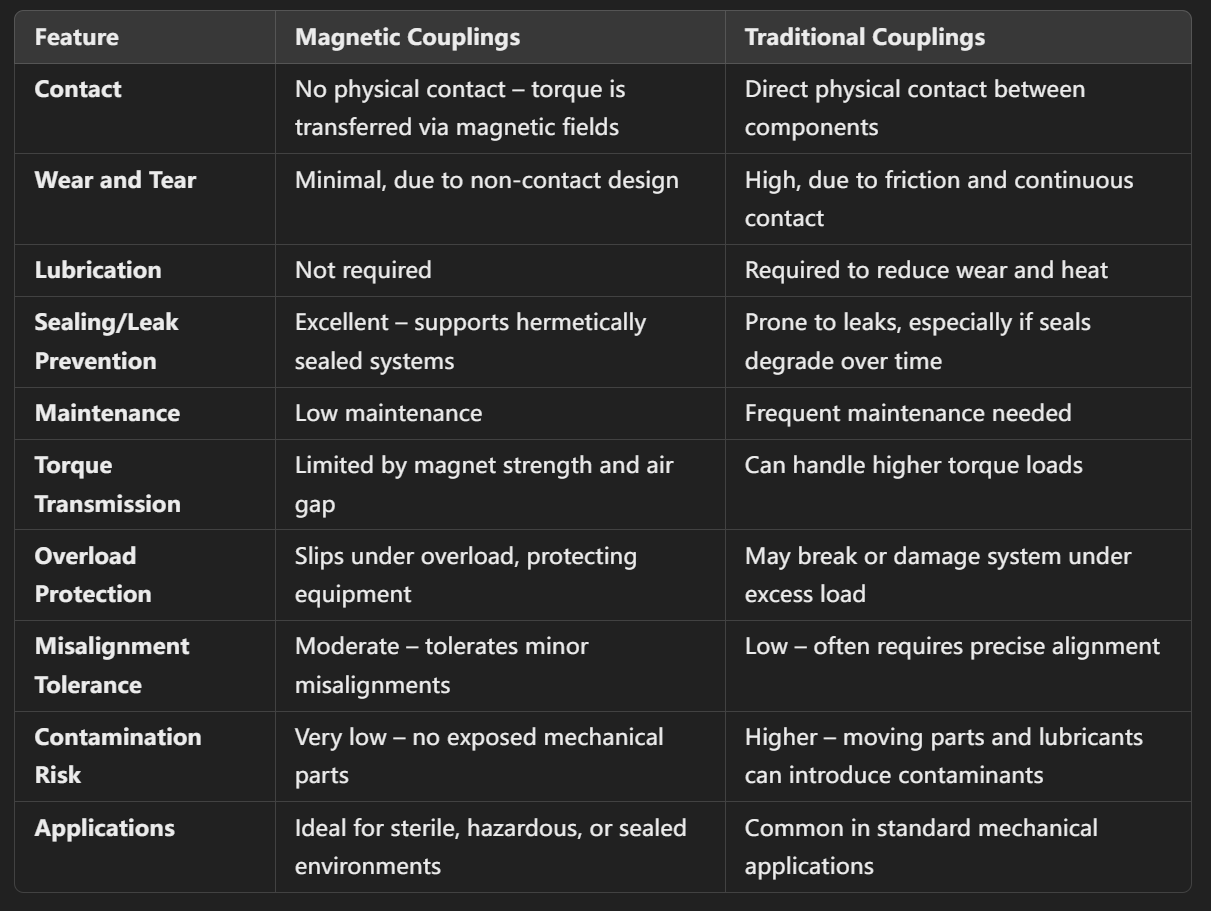
7. How Neodymium Magnetic Can Be Used in Magnetic Couplings
Neodymium magnets, known for their exceptional magnetic strength, are commonly used in magnetic couplings. Their high magnetic flux density allows for the transmission of significant torque across air gaps, making them ideal for compact and efficient coupling designs. Additionally, neodymium magnets’ resistance to demagnetization ensures reliable performance over time.
8. Conclusion
Magnetic couplings represent a significant advancement in torque transmission technology, offering contactless power transfer that enhances equipment longevity, reduces maintenance, and ensures leak-free operation. The application of magnetic coupling across diverse industries underscores their versatility and effectiveness in scenarios where traditional couplings may fall short.
9. FAQs
Q1: Can magnetic couplings handle high-torque applications?
A1: Magnetic couplings are suitable for moderate torque applications; however, their torque capacity can be increased by using stronger magnets or optimizing the coupling design.
Q2: Are magnetic couplings affected by temperature changes?
A2: Yes, extreme temperatures can affect magnet performance. Selecting magnets with appropriate temperature ratings, such as certain grades of neodymium or samarium cobalt magnets, can mitigate this issue.
Q3: How do magnetic couplings accommodate misalignment?
A3: Magnetic couplings can tolerate minor misalignments due to the flexible nature of magnetic fields, reducing stress on connected components.
Q4: Do magnetic couplings require special maintenance?
A4: Generally, they require less maintenance than mechanical couplings due to the absence of physical contact and wear.